作者 | 邱锴俊
编辑 | 邱锴俊
蜂巢能源亮相之时,打出 「叠时代」 旗号,要以叠片工艺打天下。从此,VDA 电池,叠;MEB 电池,也叠。
2021 年蜂巢能源电池日,蜂巢宣布将其电池全系 「短刀」 化。所谓 「短刀」,是薄长条形方壳电池,最长将近 600 mm。
这么长的电芯,叠起来很难对齐。还叠吗?
还叠。
而且速度还要提升,要能和大多数方壳电池厂的卷绕工艺 PK。
真能做出来吗?
2 月 25 日,我有机会走进蜂巢能源常州工厂二期的 「短刀」 产线,见证 「短刀」 生产的过程;此后,又和蜂巢能源董事长杨红新等高管交流电池的研发和生产。
「‘短刀’的产线和全球其他所有电池产线比,都是非常先进的…… 我们对产线非常有信心,能造出高质量的电池。」 杨红新说。
在搞定第一代 「短刀」 的研发、生产之后,蜂巢能源还要在 「短刀」 上持续做文章:高比能的、高倍率的、材料更丰富的…… 都有布局,以应对国内外对手的持续出招。
像蜂巢能源这样的动力电池企业,很多人以为就是生产制造,并没有什么技术含量。但是,在国家战略新兴产业下,蜂巢能源研发无钴电池等新产品、研发应用叠片工艺、机器视觉、人工智能等新技术,都是全球科技前沿的拼争,也面向蓬勃发展的电池市场需求。
无论是研发还是生产,这都是妥妥的硬科技,也是支持蜂巢能源快速增长的核心动力。
「短刀」 良率近 90%
蜂巢能源 2018 年 2 月成立。首个工厂落地常州,2019 年底一期就建成;2021 年三季度,二期又建成投产。速度很快。
二期 8GWh 产能中,其中有一条是蜂巢能源特别看重的 「短刀」 产线。蜂巢希望用 「短刀」 品类,来兼容乘用车、商用车、储能等市场的需求。

「短刀」 绝对是蜂巢能源战略级别的产品。
和比亚迪的刀片电池相比,蜂巢能源的 「短刀」 也是长薄型铝壳电芯,但是长度较短,不到 600mm,而比亚迪刀片长度可达 960mm。
蜂巢能源认为,「短刀」 有刀片电池的几乎所有长处:体积能量密度高、可以作为结构件做 CTP,降低成本,易于散热,安全性好。
此外,由于它的长度还不是太长,能够适配 80% 以上的乘用车,包括和大众系推行的 MEB 模组相兼容,还适合做储能。另外,生产工艺也更好实现,做到更高的良品率。
这一切都是理论推导,2018 年才成立的蜂巢能源,真的能将长达 600mm 的电芯做好吗?
任务落在蜂巢能源常州工厂二期。
2021 年三季度,蜂巢能源常州工厂二期投产,可以生产三种规格的电池:VDA、MEB 和 「短刀」。
无论是哪种电池,生产工艺流程大致类似,分为匀浆、涂布、辊压、切片、叠片(或卷绕)、装配、注液、化成等。
一般的电芯生产流程

就蜂巢能源的 「短刀」 品类而言,难点在于涂布、辊压、模切和叠片等工序。因为长度达到近 600 mm,涂布的面密度和对齐度就有很大难度;模切过程类似,要切得非常精准;而叠片工序,必须叠得很快,还要叠得很齐。
在涂布工段,我们参观了正极涂布工序。这一工序中的涂布机,能够分两列涂 1.4 米。蜂巢能源董事、工艺资深总监刘小安介绍,这是业界最宽的涂布机之一。
评价涂布工序的好坏,主要是三个指标,速度、面密度和涂布位置的准确度。蜂巢 「短刀」 的涂布工序能做到的水平是:涂布速度到 80 m/min 的水平,涂布面密度控制在 ±1.5% 以内,涂布正反面错位≤0.5 mm。
刘小安说,这几个指标都是业界最好的水平。

在涂布之后,需要对极片进行辊压,以确保正负极和基材紧密贴合,以及实现高能量密度。「短刀」 片的极片很长,辊压难度也大,因为必须做到整个极片的高度、密度都高度一致。
这一工序段还有一个难点,在辊压过程中,料区的铝箔片和无料区的铝箔片,应力不一样,容易发生断带。
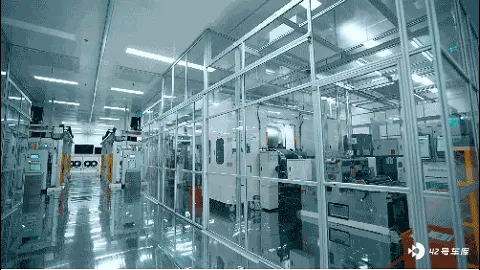
这需要铝箔很好的延展性。铝箔在被加热的情况下,会有更好的延展性。业界一般的解决方案是热辊压,即辊压机是加热过的。蜂巢的辊压工序特别之处是,提前通过电磁加热,加大铝箔延展性,因为仅仅辊压时加热,效果有限。
在辊压环节,蜂巢能源 「短刀」 的 CPK 做到大于 1.33(相当于该工序段产品的理论合格率 = 99.993%)。
在模切环节,和蜂巢能源一期产线不同,二期蜂巢都采用了激光模切工序。激光模切精准度更高,产生毛刺小,也不用模具,速度也更快。这一模切线相比一期,从每分钟切 30 米,提升至 40-50 米。
切片之后,就到了蜂巢最核心、也最有竞争力的叠片工序了。在国内,方形铝壳技术路线的企业,一般都采取卷绕工序,因为速度快,设备也较为简单。叠片工序原来一般用于软包电池。
但是,叠片电池的安全性更好,能量密度也更高。因此蜂巢刚刚亮相,就确定以叠片为技术路线,并成为高速叠片工艺的引领者。
在一期,蜂巢能源已经实现了业界最快的 0.6 秒 / 片的叠片速度。在二期,蜂巢 Z 字形叠片机,已经实现了 0.4 秒 / 片。另外,在二期产线一个被围挡起来工序上,蜂巢再进一步,实现了 0.125 秒 / 片的叠片速度。
刘小安说,0.125 秒 / 片的叠片速度已经可以叫板卷绕工艺。一般卷绕的速度是 0.2 秒 / 片。
叠得快的同时,还得叠得准。刘小安介绍,现在 「短刀」 叠片工序的对齐度精度是 ±0.3mm,达到了业内最好的水平。
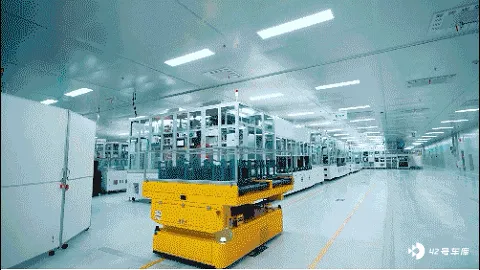
在叠片工序之后,叠好的极组要送去装配。在这两个工序衔接的物流段,蜂巢能源采用了业界首创的磁悬浮物流线。和传统的皮带物流线相比,磁悬浮物流线速度快达到 3 米 / 秒的速度,是业界一般水平 ——0.3 米 / 秒的十倍,而且异物抑制率提升了 80%。
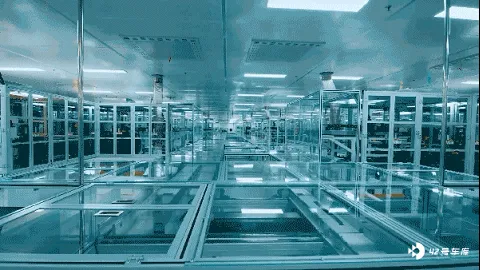
一方面是磁悬浮物流线没有传送摩擦,不会带来粉尘污染;另一方面,是蜂巢还采用了 AI 技术,来设置磁悬浮托盘的加速、减速,防止撞击。
叠片之后的极组,再经过热压、装配、注液、活化、老化、检测等环节就宣告完成。
「短刀」 也就此诞生。
目前,方形电池越做越大已经成为潮流,因为能够提升能量密度,并且和底盘结合,部分作为结构件使用。很多企业也采用长薄形电芯,但是要么做不了那么长,要么良品率上不去。
蜂巢能源常州工厂二期的 「短刀」 产线,不仅能够将长达 600mm 的 「短刀」 生产出来,而且良品率也不错。
杨红新介绍,现在 「短刀」 产线还处在爬坡阶段,但良品率已经到 85-90% 的水平。「我们的目标是能够做到和传统的产品一样的水平 ——95% 以上。」
硬科技成就智能制造
蜂巢能源 「短刀」 产线,不仅是全球最先进的电池生产线,也是智能制造的典范。
首先,这个产线应用了很多电池生产所需的高端装备。
最典型的就是超高速叠片机。在蜂巢能源一开始打出 「叠时代」 口号时,还是从韩国寻找先进的叠片技术和设备。但是二期即将启用的超高速刀片式电芯叠片机,就是蜂巢能源自己研发设计,委托设备厂加工的。
前面提到,这个叠片机叠片效率可以做到 0.125s / 片,超越普通卷绕工艺的效率,引领了全球叠片工艺的进步。
此外,在匀浆工序中,蜂巢采用了 2300L 大容量双行星搅拌设备。刘小安介绍,这个设备的单体容量在行业里是最大的,每罐浆料可生产纯电动车约 10 辆左右。
其次,这个产线大量应用了机器视觉,帮助实现工业自动化和智能化。
「短刀」 产线主要用了三种机器视觉设备:β 射线检测系统、激光检测和 CCD(影像)检测。
β 射线检测和激光检测是对检测对象发出 β 射线或者激光,通过检测 β 射线衰减情况或者是激光反射数据,来分析、测量检测对象的厚度、大小、位置等数据。
而 CCD 检测,就如同给被检测对象拍了一张照片,然后将图像信号转换为数字信号,再通过系统对信号进行运算,来判别被检测对象的特征。
蜂巢能源大量应用这些设备,来监测监测电芯生产品质。
比如在涂布工序上,蜂巢采用 3 套 β 射线在线面密度检测系统和 2 项 CCD 实时涂宽检测系统,来确保面密度的一致,以及涂布位置的准确性。
再比如,在辊压工序,蜂巢采用了实时在线激光测厚技术,帮助辊压厚度控制在 ±3 微米以内。
还有,在模切工序上,蜂巢采用 2 套 CCD 检测极片的白点、黑点、划痕,以及尺寸是否符合要求。
对于人眼不能看出来的问题,机器的视觉可以做到无论巨细,都一览无遗,帮助把控产品质量。

第三,蜂巢能源 「短刀」 产线大量采用了人工智能(AI)技术。
在蜂巢能源开始规划建厂时,就以建设车规级动力电池为标准,而要做到车规级,就必须大量采用 AI 技术。
AI 要发挥作用,参照人类的智能,首先它要像人一样,能有感官来获取信息,因此,产线必须实现高度数字化,让人工智能充分掌握产线的信息。
蜂巢能源在这一方面,通过人、机、料、法、环、测、时间等 7 维制程管控,实现过程超过 2500 个因子的监控,并可追溯到单电芯每个制程的过程数据。这些数据在手,AI 对产线就一览无遗了。
AI 发挥作用的第二步,是学习。通过大数据的分析,AI 逐步建立 2500 个因子的参数,和产品质量、数量的关系。这一过程中,蜂巢并不依赖它的供应商西门子,而是建立了自己的算法团队,通过构筑各种模型,来训练 AI。
AI 发挥作用的第三步,是智能反馈、持续调优。在找到各个因子和产品质量、数量关系之后,AI 就能寻找最佳参数组合,来提升质量或者效率。
举例而言,在涂布工序中,β 射线检测系统和 CCD 涂宽检测系统与涂布机是实时互动的。一旦检测设备发现了面密度和位置的异常,就会自动调整涂布参数,让涂布机执行,使其达到生产的要求。
当前,电池生产也已经成为不同企业、甚至不同国家争相布局的业务。设备的先进水平、智能化水平,则是判断电池工厂的两大标准。目前,蜂巢 「短刀」 工厂,智能制造水平是领先的。
特别是人工智能。先进的设备可以购置或者模仿学习,但是人工智能的布置和进化,需要时间和积累。
持续进化的 「短刀」
蜂巢能源现在的 「短刀」 产线,生产的是磷酸铁锂电池,能量密度达到 175 Wh/kg。第二代 「短刀」,能量密度能做到 190 Wh/kg。
能量密度的竞争,只是电池竞争的一项。伴随电动汽车等应用场景的需求,电池还需要在快充倍率、材料供应的稳定和经济、高安全性等许多方面展开竞争。
蜂巢能源的 「短刀」 如何应对呢?
蜂巢能源的策略是,在坚持 「短刀」 这一规格体系的基础上,不断研发、应用新的材料技术,以应对不同的需求。
在能量密度提升方面,蜂巢既有和同行类似的方案,也有自己坚持的方案。
「不管是磷酸铁锂混磷酸锰铁锂,还是磷酸锰铁锂混三元,我们也都在做。」 杨红新说。
他介绍,采用类似技术,蜂巢 2023 年就会推出第三代 「短刀」,能量密度会进一步提升。
杨红新介绍,磷酸铁锰锂等技术实现了较高能量密度,对三元电池和无钴电池也提出挑战。
蜂巢的应对方案是,三元电池仍然坚持中镍路线,但是提升中镍的克容量和电压。「我们 2022 年上半年就会量产 4.4V 中镍高电压产品。无钴 4.4V 的产品也会在今年年底、或 2023 年的年初量产。」
杨红新说,通过提升电压、提升材料整体克容量,三元 「短刀」 能量密度有望达到 250wh/kg,可以铁锰锂、铁锂拉开一定的差距。
在快充性能方面,蜂巢能源的提升路线图是:「我们接下来所有的‘短刀’,1.6C 是标配,我们正在开发 2C-2.2C 的铁锂,我们也在预研 4C 的磷酸铁锂。」
除此之外,杨红新透露,蜂巢能源在研究硅负极,也在开发固态电池技术、钠离子电池正极、负极、电解液等等。

对于电池材料的创新和进化,杨红新认为,「这就是做电池有意思的地方,但是小企业会跟不上,因为要同时开发五代、六代产品,十几种体系配合到一起。庞大的投入,资源的需求,人才的需求,未来几年以后才会见效益,只有像我们这样重视研发,有一定资源的公司才能够坚持下去,很多小企业是没有办法全面开花做这件事情的。」
确实,当前的电池产业,早已不是资源密集型产业,也是技术密集型产业。无论研发和生产,都需要巨额的研发投入,生产设备、工艺创新和应用的投资。这使得电池企业的存活门槛,会越来越高。
2022 年,蜂巢能源的 「短刀」 电池,出货量有望超过 2GWh,为其全系 「短刀」 化打开局面。
「短刀」 能够挥舞多久?要看蜂巢能源持续研发和生产创新。
研发方面,蜂巢能源第二代、第三代 「短刀」 的研发已经进行。生产方面,首个 「短刀」 产线建成投产后,蜂巢能源已经积攒了经验。下一个 「短刀」 产线,良率会更高、效率也会更高。